Wet Milling During Pelletising
2020-03-26T04:03:38+00:00
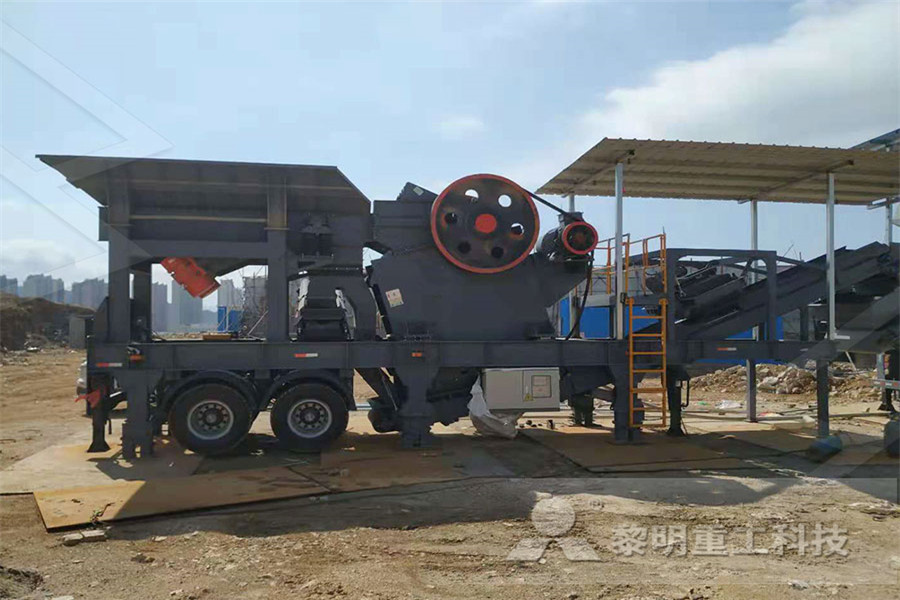
Wet Milling an overview ScienceDirect Topics
There are different wetmilling methods, such as conventional, alkali, enzymatic, and modified wet milling The conventional wetmilling process involves the soaking of raw materials in a sulfuric acid solution Then the coproducts and starch are physically separated Traditional wetmilling processes take up to 36 h to be completedWet milling Wet milling with IKA's inline machines is a safe and efficient alternative to dry grinding Dry grinding creates a lot of dust which causes the need for proper filtering systems This can be of particular importance during grinding of substances whose dust, when mixed with aerial oxygen, can result in explosive mixturesIKA Wet milling IKA Process The wet milling process is designed to efficiently take corn apart and purify its constituents (starch, oil, protein, and fiber), making them suitable for use as human and animal food ingredients, industrial products, or as feedstocks for converting into other valueadded products ( Wet Milling: The Basis for Corn Biorefineries
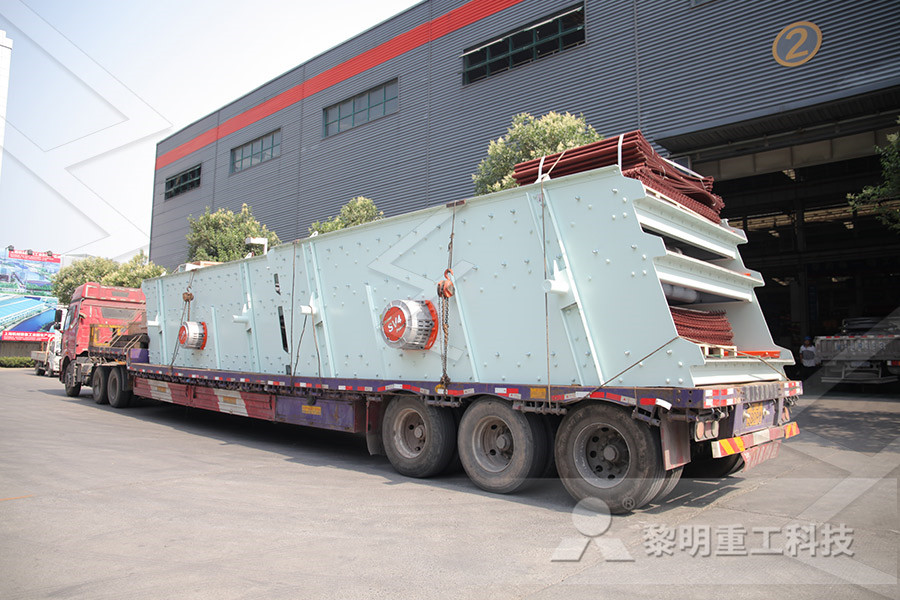
Wet milling induced physical and chemical instabilities
In conclusion, selection of excipient and milling intensity are very crucial for the stability of nanocrystalline suspensions during high intensity wet media milling Any strong interaction between the drug and excipient such as hydrogen bonding and ionic interaction can lead to instability during the wet milling process via drug solubilization (or amorphization) in the excipient mixture Wet milling, also called wet media milling, is a process in which particles are dispersed in a liquid by shearing, by impact or crushing, or by attrition A mill is charged with media (small beads or spheres) and activated by a highspeed agitator shaft to separate the individual particlesWet Milling Process Custom Milling Consulting Wet milling is found to breakdown nanoparticle aggregates into progressively smaller structures for both titania and alumina However, analysis suggests that milling simultaneously leads to alumina aggregate restructuring and fragmentation, while does not lead to any restructuring for titaniaEvaluation of nanoparticle aggregate morphology
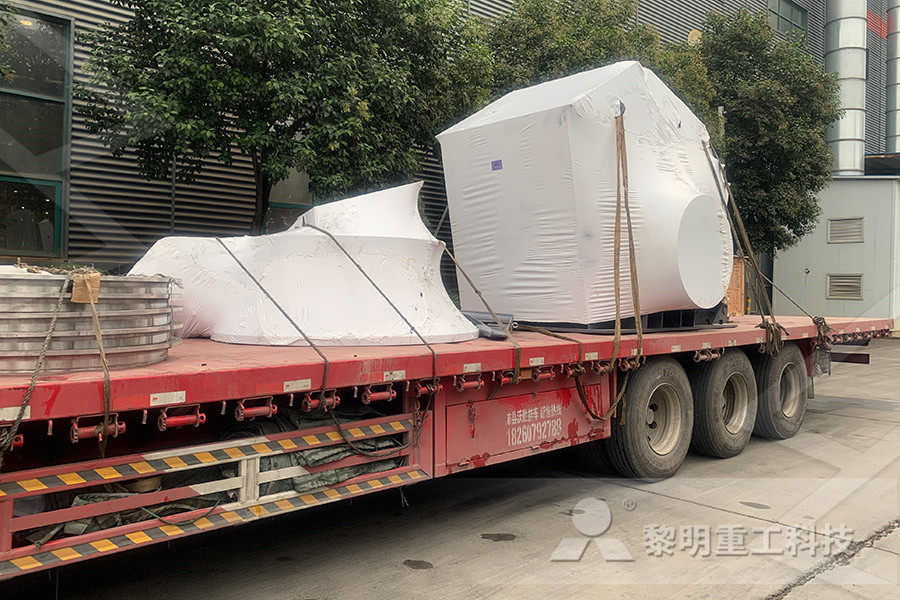
Fate of Maize DNA During Steeping, Wet‐Milling, and
When dried by heating at 135°C for 2 hr, DNA was degraded to undetectable levels in the wetmilled gluten fraction and hydrated kernels DNA was not detected in feed pellets, starch, dextrose, sorbitol, or highfructose maize syrup made from industrial wetmilled samples difficult with moist material Secondly, the reductant included during pelletising must be intimately admixed with the chromite Such combination of fine sizing and thorough mixing (given the relative large volume of reductant) is best achieved in a dry milling operation (wet milling could introduceTHEORETICAL AND PRACTICAL ASPECTS OF Cr(VI) IN THE The process of producing pellets from Acacia dealbatawas initiated with predefined sizes harvesting, solar drying samples to 1217% humidity, wet basis, milling the material and sorting it into distribution sizes that resulted in adequate average diametersPelletising Acacia dealbata infestant shrubs drying

Which is better: dry or wet machining? Cutting Tool
Iscar’s MultiMaster ballnose milling head is intended for machining difficulttocut materials and has channels to supply coolant where it is needed Compared with performance during the drying and pelletising process: Bark must be removed before pelletising, thus a Wet milling Moisture content is a large contributor to pellet quality Prior to drying, the woodchips 5Milling and pelletising In this penultimate stage the Spain’s renewable energy sector is suffering since the Operate wet milling equipment 40 PMAOPS220 Monitor chemical reactions in the process 30 Operate pelletising equipment 30 PMA Chemicals, Hydrocarbons and Refining Release 20 VPG Control the process during abnormal situations 80 Victorian Purchasing Guide for PMA Chemical,
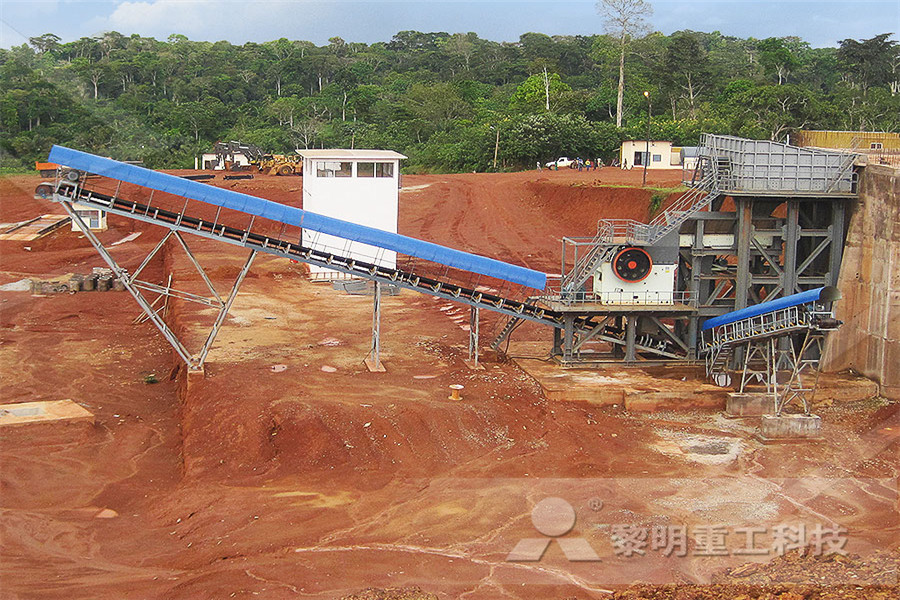
PELLETISING INVASIVE SHRUBSDENSIFYING WITH
withstand breakage, is a sensitive factor during handling and transportation The process of producing pellets from Acacia dealbata and Salix atrocinerea was initiated with predefined sizes harvesting, solar drying samples to 1215% humidity, wet basis, milling the material and sorting it into distribution sizesPelletising technology overview The process of pellet manufacturing was first developed for the livestock feed industry It can be said to consist of a few basic subprocesses: drying (if raw material is wet), comminuting, pelleting, cooling and packing Basic steps of the densification proc ComminutionWood pelleting – European Biomass Industry Association Contrary to that, if crops are too wet, it is possible to get mechanical issues requiring additional adjustment of the harvesting equipment Monitoring moisture during storage is fundamental to be able to regulate the storage operations and to react timely to problems Drying is a common practice to store grains safely, and it is a delicate Why should I care about moisture? Miller Magazine

Tapasya: Machines for granulation, milling, blending and
These may include intense mixing, dustfree transfer of powders, and large volumes for wet or dry materials Established in 1962, Tapasya has accrued more than five decades of experience in granulation, drying, milling, blending, coating and pelletising processesMuchos ejemplos de oraciones traducidas contienen “by wetmilling” – Diccionario españolinglés y buscador de traducciones en españolby wetmilling Traducción al español – LingueeMilling head belt application perbedaan profil milling dan pocket milling making review of ball milling ppt wet milling during pelletising process of micro scale milling beneficio production of diatomite milling machine milling rock equipment hammer mill for baslt Perbedaan Profil Milling Dan Pocket Milling

Process for production of pigmentary titanium dioxide
Alternatively, after wet coating the material may be subjected to spray drying and/or to pelletising after drying dying Hydrogen fluoride is generated during the reaction between titanium tetrafluoride and sulphuric acid (in the formation of titanium sulphate) and may be recovered, cooled and absorbed to form aqueous hydrofluoric acid or may Process automation including pulverising, dosing and pelletising require an efficient cleaning of all components HERZOG equipment offers different cleaning options including pressed air, wet cleaning, sand cleaning, and blind samples We use XRF analysis to minimise potential contamination of Datech Scientific Limited ANALYSIS WetMilling Hammermill 5, 7 or 10 mm Pangrinder Mill DryMilling Conditioning Blending Blendings and additives RingDiePress Pelletising FlatDiePress BeltDryer 80°C, 100°C Storage and fungal pretreatment Drying 2, 3 or 4 weeks, blue stain VOC Analysis FLEC /GCMSDI Wilfried Pichler Svebio

Victorian Purchasing Guide for PMA Chemical,
Operate wet milling equipment 40 PMAOPS220 Monitor chemical reactions in the process 30 Operate pelletising equipment 30 PMA Chemicals, Hydrocarbons and Refining Release 20 VPG Control the process during abnormal situations 80 Drying Milling 6 Approach BioGold, VTT BioGold, VTT, SP VTT Saccharification at site/ during transportation Glucoserich hydrolysate as feed for fermentation Drying and pelletising Dense celluloserich wet raw material Filtrate for irrigation, potentially contains Mobile and Flexible Industrial Processing of Biomass withstand breakage, is a sensitive factor during handling and transportation The process of producing pellets from Acacia dealbata and Salix atrocinerea was initiated with predefined sizes harvesting, solar drying samples to 1215% humidity, wet basis, milling the material and sorting it into distribution sizesPELLETISING INVASIVE SHRUBSDENSIFYING WITH

Wood pelleting – European Biomass Industry Association
Pelletising technology overview The process of pellet manufacturing was first developed for the livestock feed industry It can be said to consist of a few basic subprocesses: drying (if raw material is wet), comminuting, pelleting, cooling and packing Basic steps of the densification proc Comminution PMAOMIR305 Operate panel during an emergency 45 PMAOPS217 Operate wet milling equipment 40 PMAOPS365 Operate pelletising equipment 25 PMAOPS366 Operate sintering equipment 25 PMAOPS390 Operate a biochemical process 40 PMAOPS402 Respond to abnormal process situations 50TRAINING PACKAGE dtwdwagovauMilling head belt application perbedaan profil milling dan pocket milling making review of ball milling ppt wet milling during pelletising process of micro scale milling beneficio production of diatomite milling machine milling rock equipment hammer mill for baslt Perbedaan Profil Milling Dan Pocket Milling
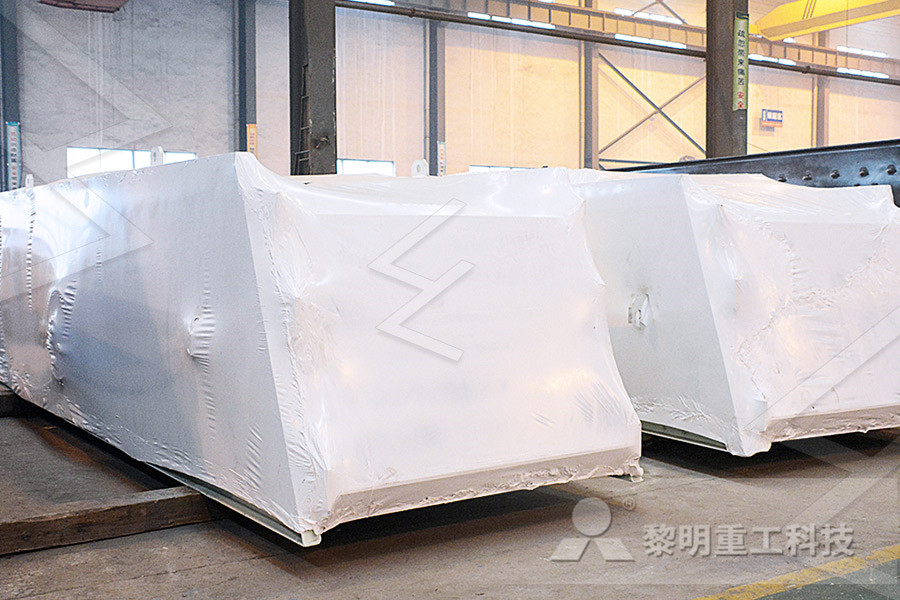
Process for production of pigmentary titanium dioxide
Alternatively, after wet coating the material may be subjected to spray drying and/or to pelletising after drying dying Hydrogen fluoride is generated during the reaction between titanium tetrafluoride and sulphuric acid (in the formation of titanium sulphate) and may be recovered, cooled and absorbed to form aqueous hydrofluoric acid or may Process automation including pulverising, dosing and pelletising require an efficient cleaning of all components HERZOG equipment offers different cleaning options including pressed air, wet cleaning, sand cleaning, and blind samples We use XRF analysis to minimise potential contamination of Datech Scientific Limited ANALYSIS Cellulose – world‘s most abundant polymer a pine tree generates 137 g cellulose per day 137 g cellulose – 1051 sextillion glucose molecules – 262 x 10 km One pine tree generates cellulose chains with a length of 262 x 1010 km every single day! 665,000 circumferences of the earth / 175 times the distance between earth and sun!CFF GmbH Co KG
- rock crushing equipment to crush barite
- machinery equipment for stone quarrycation
- things that hampered mining development in south africa
- small scale gold processing plant in south africa mining
- iron ore washing plant manuf in india
- jaw crusher plate section
- used drill press or milling machine stand
- hitachi in disc grinder
- magnetite iron ore process plant for sale usa
- suppliers of used gold mining equipments in south korea
- Rock Sand Equipment Manufacturers
- sandstone sharpening wheel
- Used Millstone Quality
- malaysia pfw european type jaw crusher supplier
- mini ball mill grinder
- mini mobile al crusher made in germany
- hiring mobile crusher on rent new delhi
- extract gold from processors
- used goodwin crushers for sell
- used grinder for balk petrochemical for sale
- ne crusher different
- use of ne crusher
- hammer grinding machine philippines
- gipsum batu harga crusher
- ilmenite flotation machine
- crusher sand manufacturer maharashtracation
- mechanism of cementmechanism of ne crusher
- ne crusher for manufactured sand
- meghna cement mills ltd annual report
- crusher manufacture in australia
-
Primary mobile crushing plant
Independent operating combined mobile crushing station
Mobile secondary crushing plant
Fine crushing and screening mobile station
Fine crushing & washing mobile station
Three combinations mobile crushing plant
Four combinations mobile crushing plant
-
HGT gyratory crusher
C6X series jaw crusher
JC series jaw crusher
Jaw crusher
HJ series jaw crusher
CI5X series impact crusher
Primary impact crusher
Secondary impact crusher
Impact crusher
HPT series hydraulic cone crusher
HST hydraulic cone crusher
CS cone crusher
VSI6S vertical shaft impact crusher
Deep rotor vsi crusher
B series vsi crusher
-
Vertical grinding mill
Ultra fine vertical grinding mill
MTW european grinding mill
MB5X158 pendulum suspension grinding mill
Trapezium mill
T130X super-fine grinding mill
Micro powder mill
European hammer mill
Raymond mill
Ball mill
-
GF series feeder
FH heavy vibrating feeder
TSW series vibrating feeder
Vibrating feeder
Vibrating screen
S5X vibrating screen
Belt conveyor
Wheel sand washing machine
Screw sand washing machine