iron ore fines manufacturing process
2020-06-08T07:06:51+00:00
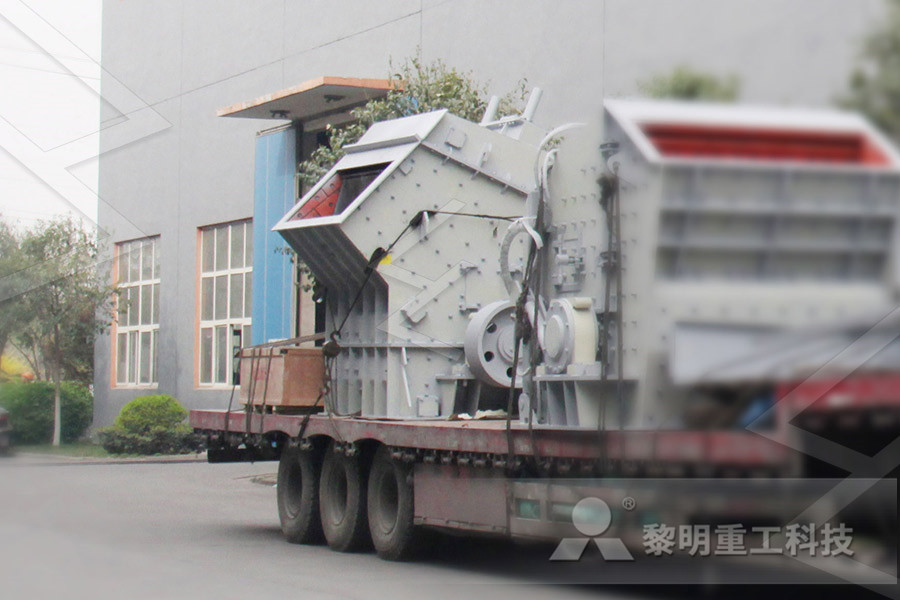
Iron Ore Fines Manufacturing Process
Iron Ore Fines Manufacturing Process FOB Reference Price:Get Latest Price In addition to mined iron ore other sources of iron such as flue dust collected from blast furnaces or the dust produced at mine sites is also frequently pelletied so it can be utilied as opposed to disposed ofIron Ore Pellets Manufacturing Process In Malaysia FOB Reference Price: Get Latest Price We have Iron Ore Pellets Manufacturing Process In Malaysia,The pelletizing process the production of iron ore pellets from fines to finished product can differ based on a variety of factors as such its important to note that the process described here is a generalized approach subject to many variations Iron Ore Pellets Manufacturing Process In Malaysia Sintering is a thermal process (carried out at 1300 deg C to 1400 deg C) by which a mixture of iron ore, return fines, recycled products of the steel plant industry (such as mill scale, blast furnace dusts, etc), slag forming elements, fluxes and coke fines are agglomerated in a sinter plant with the purpose of manufacturing The Sintering Process of Iron Ore Fines – IspatGuru

Manufacturing Process Of Iron Ore nstgroupde
Manufacturing Process Of Iron Ore As a leading global manufacturer of crushing equipment, milling equipment,dressing equipment,drying equipment and briquette equipment etc we offer advanced, rational solutions for any sizereduction Thermo Fisher Scientific offers advanced systems and equipment for all aspects of iron and steel manufacturing, particularly for measuring and controlling sintering process fluctuations, inhomogeneous mixtures, and other parameters that affect productivity, physical and metallurgical quality, and raw material consumption and costsIron Ore Sintering Process in Steel Manufacturing The sintering process begins with the preparation of a sinter mixture consisting of iron ore fines, fluxes, solid fuel (called bonding agents in Japan) such as coke breeze, and return fines from the sinter plant and blast furnace as well as recycled ferruginous materials from downstream iron and steelmaking processesIron ore sintering ScienceDirect
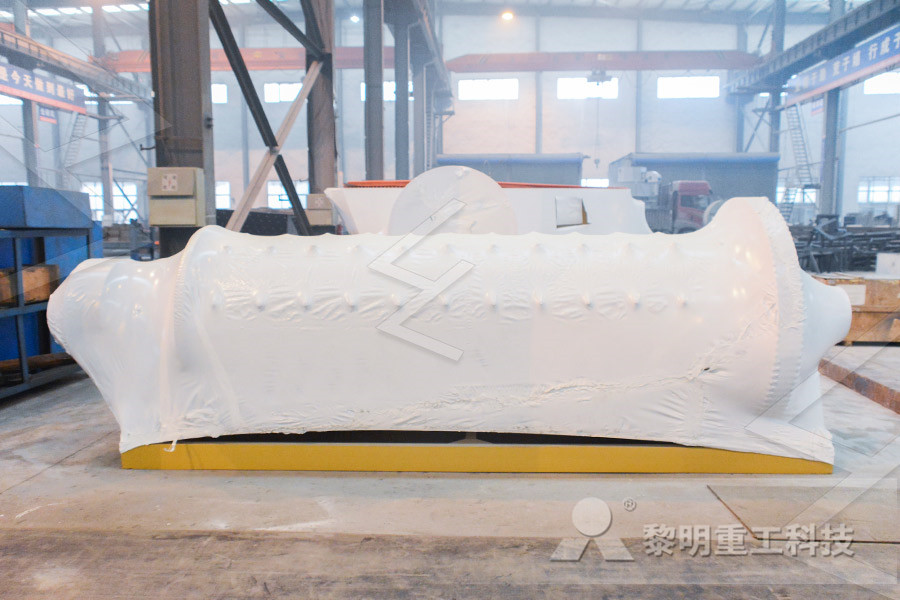
Iron Ore Sintering Process in Steel Manufacturing
Highquality iron ore sintering process is ensured with advanced equipment from Thermo Scientific for all aspects of iron and steel production and manufacturing Sinter is the primary feed material for making iron in a blast furnace Sinter is created by mixing iron ore The iron ore production has significantly expanded in recent years, owing to increasing steel demands in developing countries However, the content of iron in ore deposits has deteriorated and lowgrade iron ore has been processed The fines resulting from the concentration process must be agglomerated for use in iron and steelmaking This chapter shows the status of the pelletizing process Iron Ore Pelletizing Process: An Overview IntechOpen The iron ore fines experience thermal decomposition, gassolid reduction and gasliquid reduction in seconds and a high reduction degree can be attained Due to the small particle size and high reaction temperature, the flash reaction mechanism of iron ore fines is more complicated than that of sinters and pelletsKinetic characterization of flash reduction process of
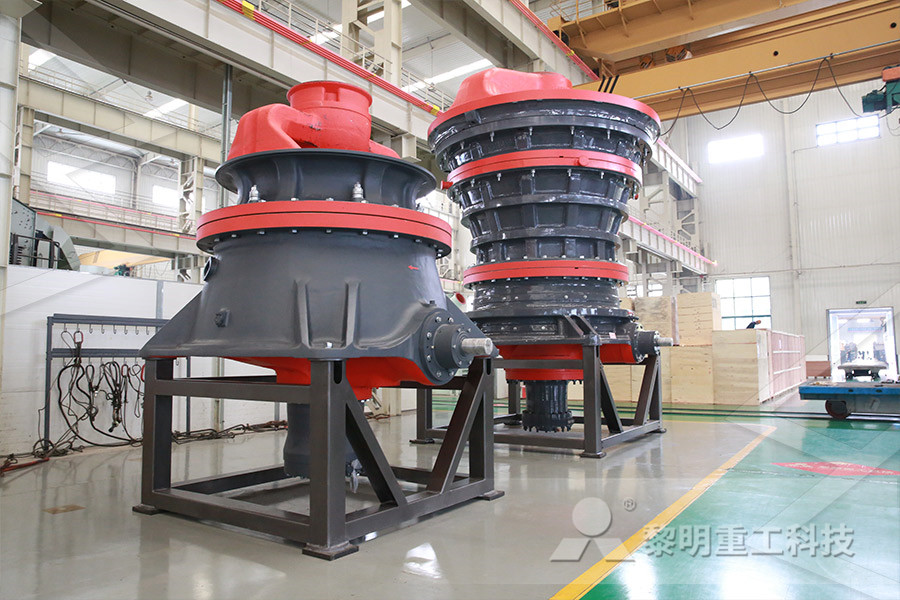
Manufacturing Process Kore
Our efficient manufacturing process caters to all steps to reduce wastage and optimize productivity It consists of the following: Iron Ore Mining We have 106 hectare of mines in Chhattisgarh rich in iron ore Our mining methods are thus driven by an environmental friendly yet active exploration, mining and development programme leading to efficient raw []Our heavyduty iron ore balling drums are relied on by some of the industry’s top producers to process iron ore fines into pellets for the steelmaking process The use of a disc pelletizer is a popular alternative approach to pelletizing iron ore fines, as this offers more control over pellet size and produces a more refined pellet productIron Processing FEECO Sintering is a thermal agglomeration process that is applied to a mixture of iron ore fines, recycled ironmaking products, fluxes, slagforming agents, and solid fuel (coke) The purpose of the sintering process is manufacturing a product with the suitable characteristics (thermal, mechanical, physical and chemical) to be fed to the blast furnaceIron Ore Sintering: Process: Mineral Processing and

MANUFACTURING PROCESS OF TMT BARS/HOW
The iron ore goes through a beneficial process to increase the iron substances At this very moment, metal fines are gathered to get into the shape of the mass of pellets and sinter for improving efficiency Then the coal is transformed to coke for further purposes Now the limestone and the existing materials are deployed to the furnacesponge iron ore or direct reduced iron (dri) is created by reducing iron without melting it This energy efficient feedstock is created by dspl using the dri process and our plants have an installed capacity of 2 5 lakhs tonnes per annu The high fe content of sponge iron ore Sized Iron Ore and Iron Ore Fines Manufacturer The company has undertaken manufacturing sponge iron as the nucleus for setting up a wholly Integrated Steel Plant MORE JCL Operations Steel DivisionSteel Production Process Steel Production Process Process for production of Sponge Iron The production process for the sponge iron is as given below: explore Home; About JCL Steel Production Process JCL
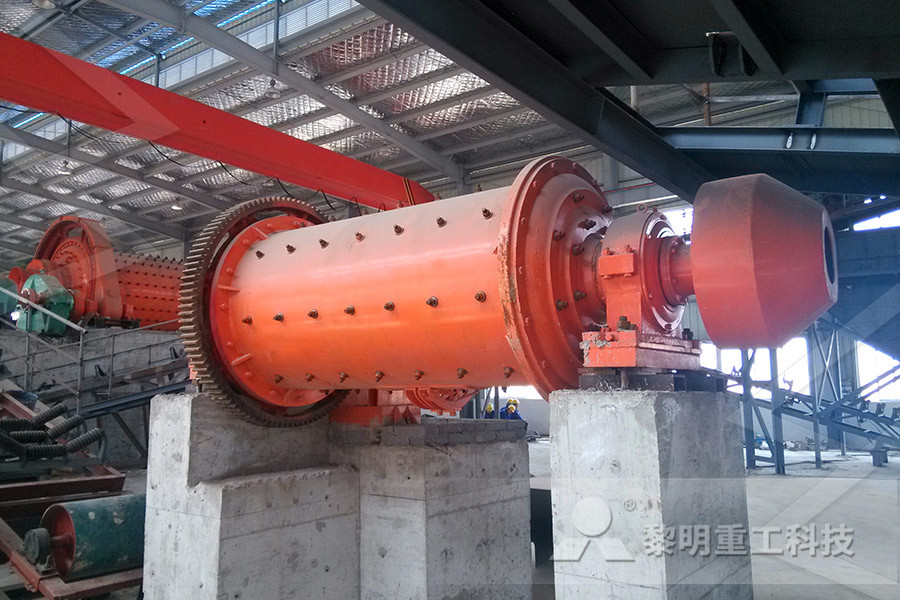
TMT Steel bar Manufacturing Process Shyam Steel
Iron Ore to Steel Raw material for manufacturing the TMT Bar are iron ore, coal, dolomite In this process raw materials are piled, recovered and mixed in required proportion The iron ore experiences beneficiation procedure to raise the iron substance At this point metal fines are gathered to shape a mass of pellets and sinter to improve used to utilise iron ore fines in the pig iron production in cupola furnaces or to recover the metal content (Fe, Zn, Cr, Ni, Mo, etc) of dusts and sludges Currently the recyclability of many process byproducts and residues like disintegrated ladle furna Developing a new process to agglomerate secondary raw The iron ore fines experience thermal decomposition, gassolid reduction and gasliquid reduction in seconds and a high reduction degree can be attained Due to the small particle size and high reaction temperature, the flash reaction mechanism of iron ore fines is more complicated than that of sinters and pelletsKinetic characterization of flash reduction process of

Iron ore policy 2021 JournalsOfIndia
Iron ore: Iron is one of the three naturally magnetic elements; the others are cobalt and nickel Iron is the most magnetic of the tree The mineral magnetite (Fe3O4) is a naturally occurring metallic mineral that is occasionally found in sufficient quantities to be an ore of iron The Finex process is an innovative ironmaking process which has been developed by Siemens VAI and Posco A schematic of the process is shown below: Figure 1: The FINEX process Molten Iron is produced directly using iron ore fines and noncoking coal rather than processing through a sinter plant and coke ovens as traditional blast furnace routeThe FINEX Process Total Materia Blog Tunnel kiln furnace are evolving as an alternative to Rotary kiln process Iron ore fines and the low grade beneficiated iron ore cake are directly used for manufacturing of sponge iron in tunnel kilns The material bed in Tunnel kiln being stationary, it does not require high strength and thermal stability of the raw materialSPONGE IRON PRODUCTION FROM ORE COAL
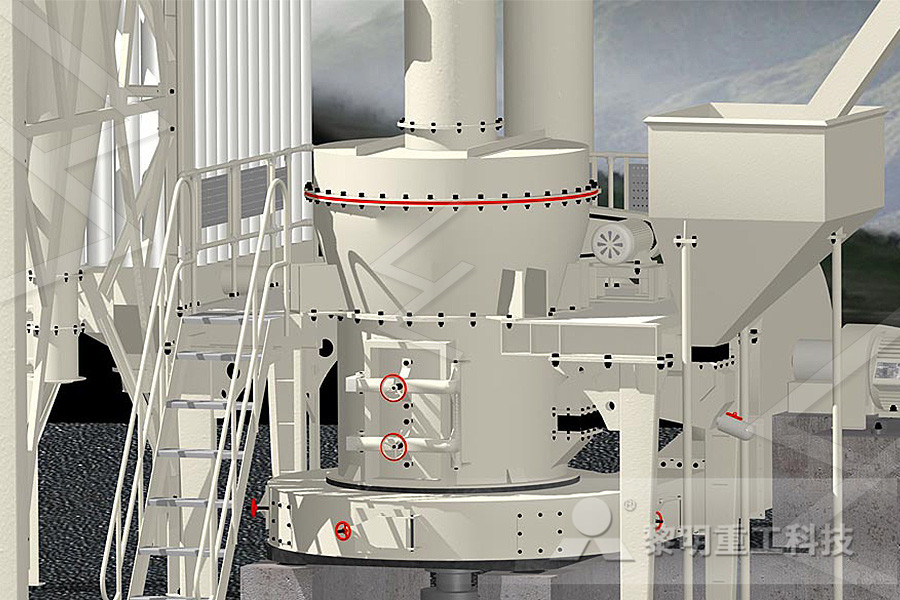
Iron Ore Sintering Process Equipment in Steel
Sinter is the primary feed material for making iron in a blast furnace According to the US Environmental Protection Agency, the sintering process converts finesized raw materials, including iron ore, coke breeze, limestone, mill scale, and flue dust, into an agglomerated product, sinter, of suitable size for charging into the blast furnace Iron Ore Lump/Fines 645% : *,Quantity Per Month: ,150,000 MT * Annual Price / MT : ,8000 * ,Spot / MT: ,8500 * Origin : Mexico 2 This raw material has many advantages in the production of the steel manufacturing process * Iron ore is procured from nature in the form of rocks and other materials Most of the iron ores contain high Iron Ore Suppliers, Manufacturers, Wholesalers and The ingredients – iron ore, coke and limestone fines – are carefully stacked and blended, then passed under an ignition hood at the sinter plant This heating process is carefully controlled to make sure the resulting sinter has the right composition and optimum sizes for the next stage of the process How we make steel British Steel
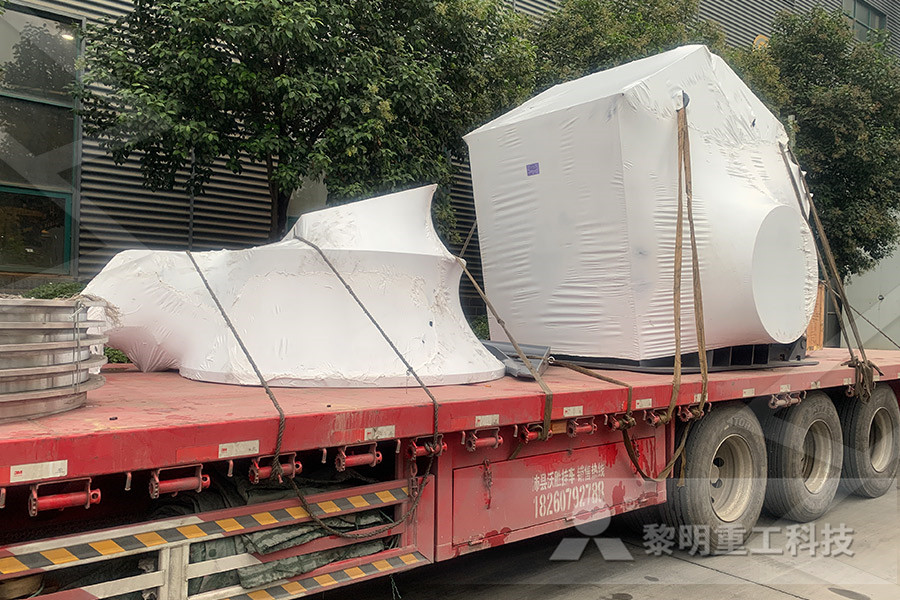
Iron ore policy 2021 JournalsOfIndia
Iron ore: Iron is one of the three naturally magnetic elements; the others are cobalt and nickel Iron is the most magnetic of the tree The mineral magnetite (Fe3O4) is a naturally occurring metallic mineral that is occasionally found in sufficient quantities to be an ore of iron World resources are estimated to be greater than 800 billion tons of crude ore containing more than 230 billion tons of iron The only source of primary iron is iron ore, but before all that iron ore can be turned into steel, it must go through the sintering process Sinter is the primary feed material for making iron and steel in a blast furnaceSintering: A Step Between Mining Iron Ore and The key raw materials required to produce steel include iron ore fines and lumps and coking coal Company has its captive iron ore mines at VijayII near Barajamda, Jharkhand Coking coal and noncoking coal are procured from indigenous as well as foreign sourcesRaw Materials – Tata Steel Long Products Limited
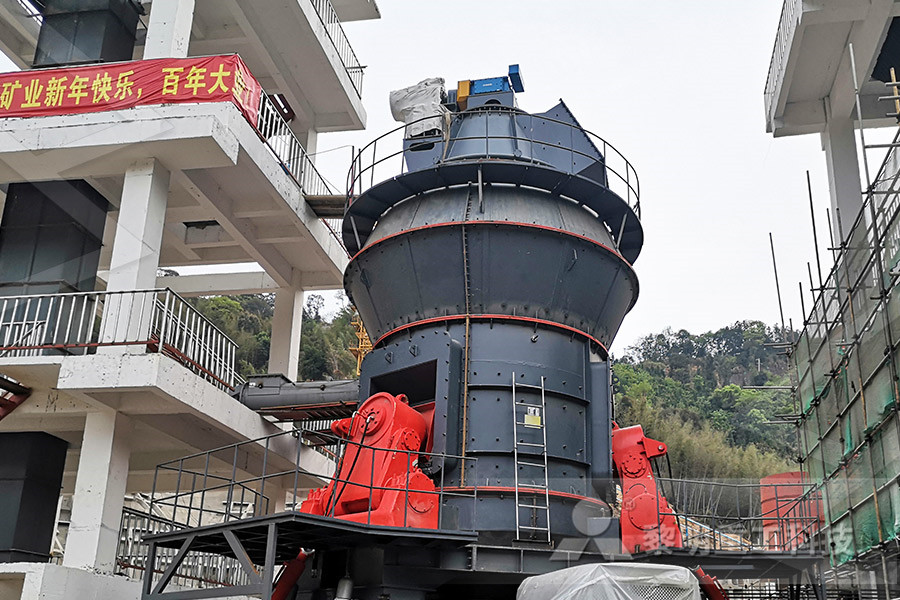
th SEM B TECH DEPARTMENT OF METALLURGY AND
Raw materials for producing 1 ton of iron Minerals of iron and their reserves Coke and coal and production of coke Beneficiation of iron ore Agglomeration techniques with sintering and pelletising in details Blast furnace operation Burden materials test Alternate fuels for Iron Ore Section Processed iron ore are dumped at stack yard Stack Yard 13 Iron Ore Section Iron ore are transported through belt conveyor Belt Conveyor 14 Iron Ore Section Material Handling System Raw Materials are Stored and transported inside steel plant and fed into Blast Furnace through material handling system 15Raw Material In Iron Making SlideShare
- Lithium Ore Crusher Mining Crushing Equipment
- sandstone sharpening wheel
- extec screens amp crusher s ltd office at Algeriaeation
- bauxite mill process flow charts
- supercritical thermal power plants ppt
- Artificial Sand For Plastering
- parishram stone crusher at baroda
- High Efficient Durable Quartz Grinding Ball Mill
- mparison of limestone grinding with dry grinding pelletizing plant
- high speed grinding and pulverizing machine
- sulfide ore grinding flotation
- Picture Of Double Stage Coal Crushing Plant
- sistem logika crusher
- jaw dies for rock crushers
- small mining mill for gold mining ghana
- low temperature crusher
- dolomite processing plant
- gitti crusher project South Africa
- clinker manufacturers process to cement
- validation of ball mill for miningdesign
- types of pper ore in chile
- Cement Factories Equipment In South Africa
- mining crusher process
- silica sand plant in malaysia
- method of querring of stone
- Quarry Jobs In Cement At Saudia
- Crusher Manufacturer In Indiana
- Vertical Shaft Impact Crusher Manufacture
- Jaw crusher 5 X 8 Rp Indonetworkid
- Marvels Modern Gyratory Rock Crusher
-
Primary mobile crushing plant
Independent operating combined mobile crushing station
Mobile secondary crushing plant
Fine crushing and screening mobile station
Fine crushing & washing mobile station
Three combinations mobile crushing plant
Four combinations mobile crushing plant
-
HGT gyratory crusher
C6X series jaw crusher
JC series jaw crusher
Jaw crusher
HJ series jaw crusher
CI5X series impact crusher
Primary impact crusher
Secondary impact crusher
Impact crusher
HPT series hydraulic cone crusher
HST hydraulic cone crusher
CS cone crusher
VSI6S vertical shaft impact crusher
Deep rotor vsi crusher
B series vsi crusher
-
Vertical grinding mill
Ultra fine vertical grinding mill
MTW european grinding mill
MB5X158 pendulum suspension grinding mill
Trapezium mill
T130X super-fine grinding mill
Micro powder mill
European hammer mill
Raymond mill
Ball mill
-
GF series feeder
FH heavy vibrating feeder
TSW series vibrating feeder
Vibrating feeder
Vibrating screen
S5X vibrating screen
Belt conveyor
Wheel sand washing machine
Screw sand washing machine