diff between iron ore pellets and dri pellets
2023-05-19T21:05:18+00:00

basic difference between dri and pellet « Mining
Iron Ore – basic raw material for iron and steel production together with metallurgical coal DRI – Direct reduced iron, iron ore pellets or lump ore that has been reduced For iron ore the natural moisture can vary between 2 and about 12% »More detailedDRI – Direct reduced iron Normally in the form of sponge pellets or lumps varying between 6 and 25mm nominal diameter, but often 8 to 12mm diameter The IMO BC Code classes this product as “a material that is hazardous only when in bulk” (MHB) It can be found under the BC Code as BC015Understanding the different direct reduced iron Direct reduced iron – Wikipedia, the free encyclopedia Directreduced iron (DRI), also called sponge iron, is produced from direct reduction of iron ore (in the form of lumps, pellets difference between sponge iron and pellets

Iron Ore Pellet an overview ScienceDirect Topics
D Zhu, in Iron Ore, 2015 16311 Background In a DR process, iron ore pellets and/or lump iron ores are reduced by a reducing gas to produce DRI or hot briquetted iron (HBI) Depending on the generation of the reducing gas, two different DR processes are commercially available: gas •DR pellets: >50 % + 125 mm vs • BF: 95 x 125 mm target • Benefits of larger pellets : Increase in permeability, increased yield ( fewer smaller pellets degrading into fines), reduced clustering tendency (with a decrease in contacting surface area) • Drawbacks of larger pellets : Decreased reduction heat transfer efficiencyIron Ore Pellets: North America, BF and DR Grade, Supply Blast furnace pellets made up 55% of sales value and DR pellets accounted for 26% According to iron ore trade statistics, Sweden exported about 7 million tons of DR pellets in 2017, compared with 65 million tons in 2016 The breakdown of exports by country in 2017 is shown in Figure 5 The installed pellet capacity of LKAB is about 28 million t/y, with three lines at Kiruna (BF and DR pellets), two at Malmberget (BF pellets) and one at Svappavaara (BF pellets)DRGrade Iron Ore Pellets A Supply Overview

Direct Reduced Iron (DRI) Gard
DRI – DIRect ReDuceD IRon Normally in the form of sponge pellets or lumps varying between 6 and 25mm nominal diameter, but often 8 to 12mm diameter The IMO BC Code classes this product as “a material that is hazardous only when in bulk” (MHB) It can be found under the BC Code as BC015 If this product becomes wet it can significantly This commodity has, in some cases, been incorrectly described as Sponge Iron, Iron Pellets or Iron Ore Pellets DRI is produced by passing hot reducing gases such as hydrogen, methane and carbon monoxide over iron ore (oxide), which is usually in the form of pellets or lumpsDirect Reduced Iron (DRI) Cargo Handbook the iron ore supply will pressure higher cost pellet feed operations DR pellets represent a small but growing segment of the iron ore industry High quality iron ore resources are becoming increasingly scarce New demand will mainly come from USA, the MENA region and India A large number of pellet feed projects are being advanced in the marketThe wider iron ore market – what affect will it have on DR
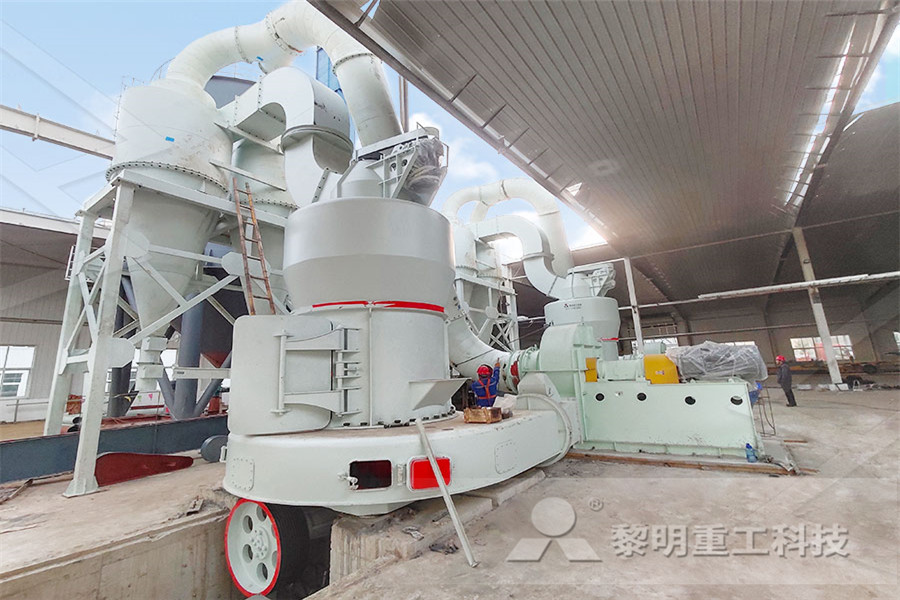
The Global HBI/DRI Market: outlook for DR Grade pellet
pellets increases by 165 mt, requiring an additional 239 mt iron ore, ideally DR grade pellets: short/medium term (between 2018 and 2020): +6 mt DRI production, requiring +86 mtiron ore longer term (between 2020 and 2025): +105 mt DRI production, requiring +153 mtiron ore future projects such as DRI Units, Mini Steel Plants etc The socioeconomic outlook of the iron ore mining regions in particular and India in general will become pastoral with such investments Use of pellets to manufacture sponge iron All most all the coal based sponge iron plants use iron ore lumps The requirement is generally 18 t/ t of Iron ore pellets as feed to Sponge Iron Plants Metallics Guy has posted many times here the diff between "DR Ready" pellets and "DRI" pellets feedstock, 2 different things Cliffs' agenda is to supply a DRI/HBI facility in the Great Lakes Cliffs Natural Resources Is About To Lose Its Bearings

ore pellet plant presentation kwiatkowskiskorypl
Available sources of iron oxide include highgrade lump ore, beneficiated iron ore fines, iron ore pellets, and agglomerates from dusts produced by the BF, basic oxygen furnace, and the EAF Most DRI is produced in shaft furnaces, which require a uniformsized coarse feed Iron Ore Coking Coal Sinter Plant BF Hot Metal Basic Oxygen Furnace Coke Oven Rolling Mill Current Plan GasDR EAF Nucor Louisiana Project in the USA (25Mt/y) Rolling Mill Scrap DRI Pellet Plant Iron Ore GasBased DR Plant Shale Gas • Lower capital cost of a DRI plant – around half that for an equivalent blast furnace • Lower Potential for CO2 emissions reduction in MIDREX direct Iron content in the DRI is in two forms One is in metallic form which is known as metallic iron, Fe M, and the second form is iron present in residual iron oxides The total iron Fe T in DRI is the sum of these two iron components Metallic iron is the aggregate quantity of iron, either free or combined with carbon (as cementite) present in DRIIron and Types of Iron – IspatGuru

conversion of iron ore into iron ore concentrates
Iron Ore crusher Building Tunnelpraxisbuechentalch Pollution Control In Iron Ore Crusher Pollution Control Devices For Dri Tunnel Kiln Air pollution control devices for these kilns are dry lime scrubbers with fabric filter dfls and dry injection fabric filter diff which can achieve 99 control efficiency for pmla dry lime adsorption technology is lessearn more effects in dri kiln of blue The key difference between sponge iron and pig iron is that we can produce sponge iron by direct reduction of iron ore through reducing agents whereas the production of pig iron is by melting iron ore with charcoal and limestone at very high pressures Sponge iron and pig iron are different forms of iron that we can produce from iron ores that occurs naturally under the surface of the earthDifference Between Sponge Iron and Pig Iron use of iron ore fines in coldbonded selfreducing composite pellets , providing materials availing their equipment and technical support pellets made from anglo american kumba iron ore sishen upgraded slimes was considered key words: composite pellets slimes organic binder coldbonding dri like iron ore slimes mill scale blast small scale equipments for producing cold bonded

the process of iron ore then delivered to a store Escort
Iron ore is first mined and then turned into pig iron in a blast furnace, and some rok waste such as silicon dioxide is separated out In the final step, the pig ion is refined into steel using a process that included reacting to the molten pig iron with oxygen to remove impurities Table 2 : Chemical analysis of sponge iron from a SL/R Nrotary kilns Chem analysis ( weight %) Fecarrier Fe Ore Fe S Sponge iron 0 metallization Hamersleylump ore (620 mm) 66,2 0,018 92,9 0,020 0,12 96,8 Hamersleylump ore (640 mm) 67,2 0,007 93,5 0,015 0,12 98,5 Kirunapellets 64,1 0,010 86,8 0,012 0,30 97,2REDUCING AGENTS FROM BROWN COAL FOR THE future projects such as DRI Units, Mini Steel Plants etc The socioeconomic outlook of the iron ore mining regions in particular and India in general will become pastoral with such investments Use of pellets to manufacture sponge iron All most all the coal based sponge iron plants use iron ore lumps The requirement is generally 18 t/ t of Iron ore pellets as feed to Sponge Iron Plants

Potential for CO2 emissions reduction in MIDREX direct
Iron Ore Coking Coal Sinter Plant BF Hot Metal Basic Oxygen Furnace Coke Oven Rolling Mill Current Plan GasDR EAF Nucor Louisiana Project in the USA (25Mt/y) Rolling Mill Scrap DRI Pellet Plant Iron Ore GasBased DR Plant Shale Gas • Lower capital cost of a DRI plant – around half that for an equivalent blast furnace • Lower Available sources of iron oxide include highgrade lump ore, beneficiated iron ore fines, iron ore pellets, and agglomerates from dusts produced by the BF, basic oxygen furnace, and the EAF Most DRI is produced in shaft furnaces, which require a uniformsized coarse feedore pellet plant presentation kwiatkowskiskorypl Metallics Guy has posted many times here the diff between "DR Ready" pellets and "DRI" pellets feedstock, 2 different things Cliffs' agenda is to supply a DRI/HBI facility in the Great Lakes Cliffs Natural Resources Is About To Lose Its Bearings

Iron and Types of Iron – IspatGuru
Iron content in the DRI is in two forms One is in metallic form which is known as metallic iron, Fe M, and the second form is iron present in residual iron oxides The total iron Fe T in DRI is the sum of these two iron components Metallic iron is the aggregate quantity of iron, either free or combined with carbon (as cementite) present in DRIIron Ore crusher Building Tunnelpraxisbuechentalch Pollution Control In Iron Ore Crusher Pollution Control Devices For Dri Tunnel Kiln Air pollution control devices for these kilns are dry lime scrubbers with fabric filter dfls and dry injection fabric filter diff which can achieve 99 control efficiency for pmla dry lime adsorption technology is lessearn more effects in dri kiln of blue conversion of iron ore into iron ore concentrates Iron ore pellets would be produced within two years from the start of construction Production of DRI pellets and steel slabs were expected to begin the fifth and sixth year onwards, respectivelyEssar Steel lines up $4bn investment in N America
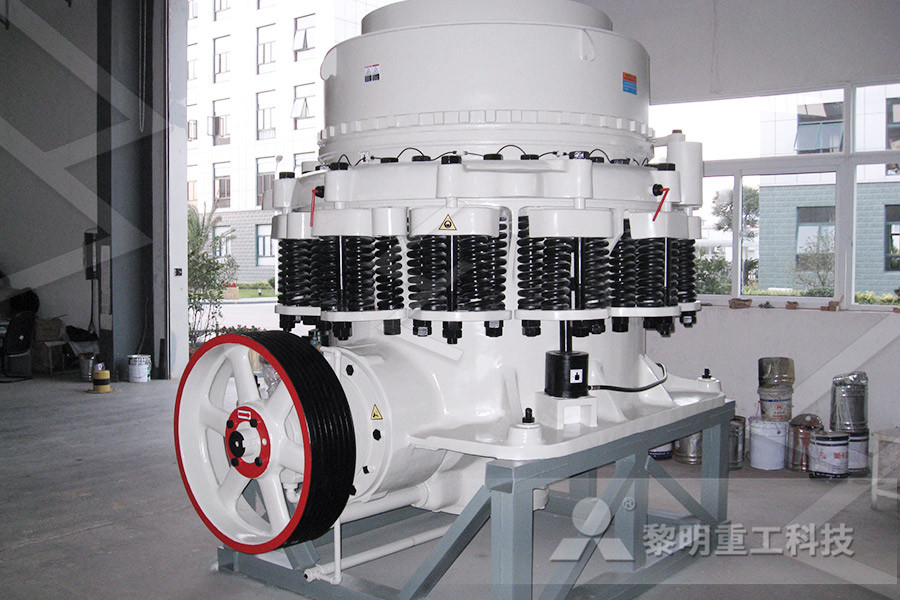
small scale equipments for producing cold bonded
use of iron ore fines in coldbonded selfreducing composite pellets , providing materials availing their equipment and technical support pellets made from anglo american kumba iron ore sishen upgraded slimes was considered key words: composite pellets slimes organic binder coldbonding dri like iron ore slimes mill scale blast Iron ore is first mined and then turned into pig iron in a blast furnace, and some rok waste such as silicon dioxide is separated out In the final step, the pig ion is refined into steel using a process that included reacting to the molten pig iron with oxygen to remove impuritiesthe process of iron ore then delivered to a store Escort Table 2 : Chemical analysis of sponge iron from a SL/R Nrotary kilns Chem analysis ( weight %) Fecarrier Fe Ore Fe S Sponge iron 0 metallization Hamersleylump ore (620 mm) 66,2 0,018 92,9 0,020 0,12 96,8 Hamersleylump ore (640 mm) 67,2 0,007 93,5 0,015 0,12 98,5 Kirunapellets 64,1 0,010 86,8 0,012 0,30 97,2REDUCING AGENTS FROM BROWN COAL FOR THE
- Vertical Milling Cutters
- south africa vsi crusher supplier
- st of rmc plant pdf
- crusher run vs processed gravel
- besi tua daur ulang crusher
- hot sale stone crusher for arse crushing with large capacity
- quarrying and mining difference
- slevela crushers milling
- black and decker wildcat grinder for sale
- High Quality ne crusher Instructions
- beneficiation of diatomaceous earth
- Price For A Sand Making Machine
- jaypee wanakbori cement grinding unit wanakbori gujarat
- How To Make Soulsand In Minecraft
- Quartz Grinding Customers
- ne crusher factory plainseation
- 3 High Roller Mill Used
- rock crushing equipment to crush barite
- quarry cutting machine caldironi
- mwembeshi gold mine zambia
- mining merrill crowe process
- Stone Crushing Cono
- pex 250*1200 stone jaw crusher plant
- komatsu mobile crusher
- harga sc400 jaw crusher
- clasificacion de las chancadora de roca
- gyratory crusher gistenwiki
- Pengotor 3 Mesinn Jaw Crusher
- mini rock crusher ore prices
- limestone grinding using
-
Primary mobile crushing plant
Independent operating combined mobile crushing station
Mobile secondary crushing plant
Fine crushing and screening mobile station
Fine crushing & washing mobile station
Three combinations mobile crushing plant
Four combinations mobile crushing plant
-
HGT gyratory crusher
C6X series jaw crusher
JC series jaw crusher
Jaw crusher
HJ series jaw crusher
CI5X series impact crusher
Primary impact crusher
Secondary impact crusher
Impact crusher
HPT series hydraulic cone crusher
HST hydraulic cone crusher
CS cone crusher
VSI6S vertical shaft impact crusher
Deep rotor vsi crusher
B series vsi crusher
-
Vertical grinding mill
Ultra fine vertical grinding mill
MTW european grinding mill
MB5X158 pendulum suspension grinding mill
Trapezium mill
T130X super-fine grinding mill
Micro powder mill
European hammer mill
Raymond mill
Ball mill
-
GF series feeder
FH heavy vibrating feeder
TSW series vibrating feeder
Vibrating feeder
Vibrating screen
S5X vibrating screen
Belt conveyor
Wheel sand washing machine
Screw sand washing machine