model of cement industry in wet process
2020-06-25T18:06:18+00:00
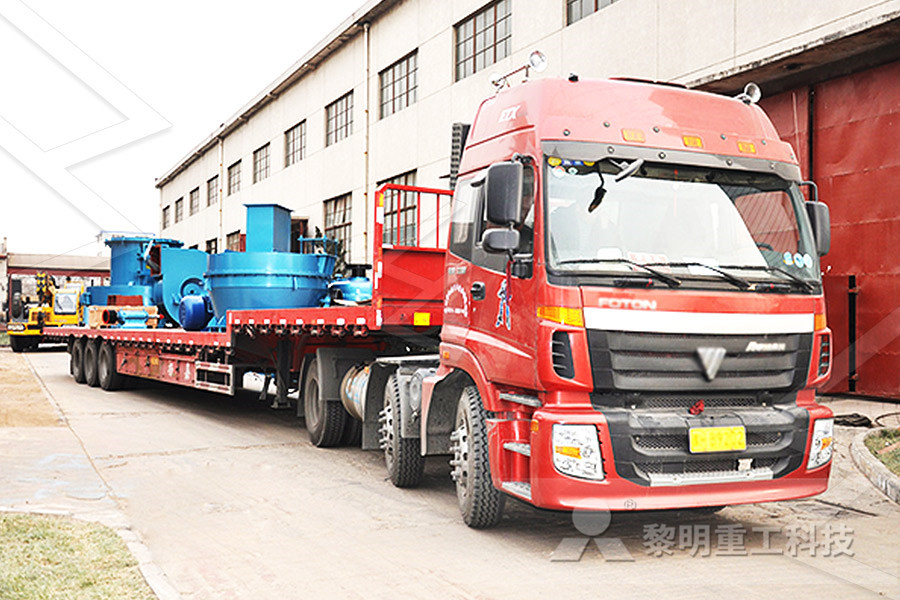
Wet Process of Cement Manufacturing Cement Wet Process
The wet process of cement manufacturing refers to grinding raw material into slurry after mixing with water and then feeding them into the wet process kiln for drying and Here is the manufacturing of cement by wet process WET PROCESS When the raw materials are soft, then the wet process is preferable to be used The cement is manufactured by the following procedure:Mixing of Raw Materials: In the wet process, there are two raw materials e calcareous and argillaceousManufacturing Of Cement By Dry And Wet Process Manufacturing process of cement: There are two types of cement process • Wet process • Dry process 6 1 Wet process: In this process, the raw materials are changed to powdered form in the presence of water In this process, raw materials are wet process of cement SlideShare

Explain dry and wet process of cement manufacturing
Wet Process The specific feature of the wet process is that the raw materials are prepared in water whereas in the dry process the materials are ground and mixed dry The flowsheet diagram of the wet process for manufacturing Portland cement is given in Figure 33 The limestone There are two different processes for manufacturing cement wet process minerals are wet ground (by adding water) to form a slurry and then dried, dry process minerals are dry ground to form a powderlike substance Both the processes Difference Between Wet And Dry Process Of Cement Wet Process of Manufacturing of Cement It is considered a better and convenient process for the manufacture of cement, especially where limestone of soft Cement Manufacturing Process: What is Cement made of

Parametric Studies of Cement Production Processes
In cement production processes, there are several models for the purpose of studying the use of alternative fuels [4, 36, 39]: phase chemistry , oxidation process of coal tar pitch , cement raw material blending process , reduction of CO 2 , sensitivity analysis of a model used for the design of rotary kiln processes , and a nonlinear model predictive control However, all these models do not address issues of real inefficiency taking place in cement Wet process kilns The original rotary cement kilns were called 'wet process' kilns In their basic form they were relatively simple compared with modern developments The raw meal was supplied at ambient temperature in the form of a slurry A wet process kiln The cement kilnProgress is particularly needed in the Eurasia region (Russia and the Caspian countries1), which has the highest thermal energy intensity of clinker production (5 GJ/t on average), primarily due to the continued use of wetprocess kilns (Beyond process technology choice, regional factors affect the thermal intensity of clinker, such as moisture content and burnability of raw materials, typical clinker composition and average cement Cement – Analysis IEA
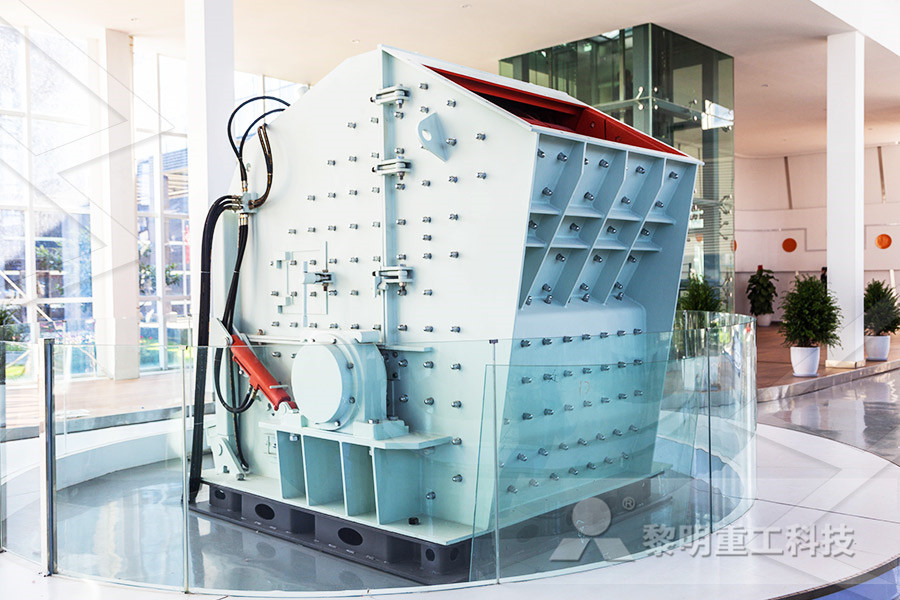
Supply Chain Management in the Cement Industry
Supply Chain Council’s SCOR model processes; plan, source, make, deliver and return In summary, the cement industry planning process is centralized and optimization oriented There is no constraint in the availability of cement main raw materials with the exception of Cement production processes are generally distinguished into wet process, semiwet process, semidry and Lepol process, and dry process For the production of clinker, the two types of kilns used are rotary kilns and shaft kilns (Hendriks et al, 2004) The world average p’s rimary energy intensity is approximately 48 MJ/kg cement, with the CHAPTER II LITERATURE REVIEW 21 Cement Industry and The knowledge of wet process kilns design and operation in the cement industry has not been improved substantially during the last decades since the precalcination process has been developed to become the technological standard In spite of the tendency to replace wet process rotary kilns for cement production by modern dry process kilns with precalcination, there are still a substantial Wet process rotary cement kilns: modeling and

Parametric Studies of Cement Production Processes
The cement industry is one of the most intensive energy consumers in the industrial sectors The energy consumption represents 40% to 60% of production cost Additionally, the cement industry contributes around 5% to 8% of all manmade CO 2 emissions Physiochemical and thermochemical reactions involved in cement kilns are still not well understood because of their complexity Cement industry is one of the six energy intensive industries in Iran accounting for 15% of total energy The model includes demand for cement, production, technologies: dry process, wet process and semidry process As mentioned before, dry process is the main technology used in IranA system dynamics model for analyzing energy Portland cement for finishing brick buildings in wet climates; Mortars for masonry construction of harbor works, etc, in contact with seawater; Development of strong concretes; A cement is a substance used for construction, where mixed with fine aggregate produces mortar for masonry, or with sand and gravel, produces concretePrimary Process Control Improvements for Cement

Modeling of Rotary Kiln in Cement Industry
Cement production is a highly energyintensive process, and the rotary kiln is the most important part of the process Having a comprehensive model of the kiln in order to reduce manufacturing costs, better performance can be created In this paper, the influence processes in a simulated cement rotary kiln and operating parameters on the output of the study were to develop and validate the Cement Manufacturing Process Phase II: Proportioning, Blending Grinding The raw materials from quarry are now routed in plant laboratory where, they are analyzed and proper proportioning of limestone and clay are making possible before the beginning of grinding Generally, limestone is 80% and remaining 20% is the clayCement Manufacturing Process Phases Flow Chart 91 Introduction The production of cement consumes approximately 32–63 GJ of energy (thermal and electrical) and 17 tonnes of raw materials (mainly limestone) per tonne of clinker produced , Energy cost accounts for 50–60% of the production costs , while thermal energy equates to 20–25% of the total production cost In the manufacturing process thermal energy is used mainly during Cement Kiln Process Modeling to Achieve Energy

Benchmarking energy utilization in cement
Nigeria is a leading producer of cement in Africa Because cement production is energy intensive, with significant adverse impacts on the environment, an apparent need exists to assess the Nigerian cement industry to identify energy use mitigation options The potentials for reducing energy use in typical Nigerian cement manufacturing plants, through the implementation of available energy There is a large cement distribution facility (now apparently closed) in West Sacramento CA, that could be represented in either N scale or HO scale using the appropriate Walthers Medusa Cement Kit A pretty accurate model could be made in N scale using the HO kit It had an overhead pipe line to deliver product to barges on the Sacramento RiverThe Cement Industry Model Railroad Hobbyist dry process cement plant and a mathematical programming model capable of suggesting the best cost effective strategy was outlined Control costs consisting of operating and investment costs along with the efficiency of control options were taken into account in the model A representative case study from the cement industry was considered inModelling the hazard control in a wet process plant a
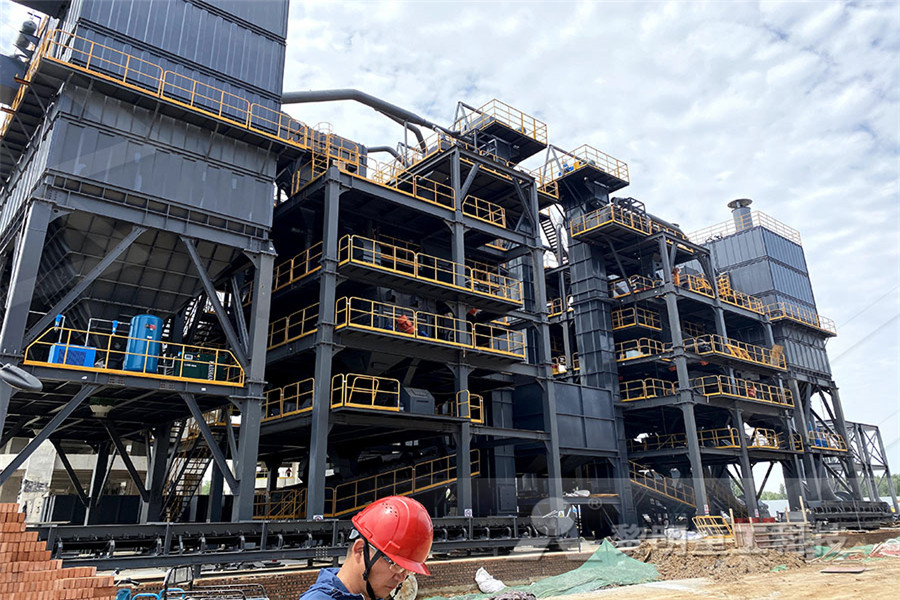
CHAPTER II LITERATURE REVIEW 21 Cement Industry and
Cement production processes are generally distinguished into wet process, semiwet process, semidry and Lepol process, and dry process For the production of clinker, the two types of kilns used are rotary kilns and shaft kilns (Hendriks et al, 2004) The world average p’s rimary energy intensity is approximately 48 MJ/kg cement, with the Cement Production Line, Cement Plant Equipment, Wet Processing Cement Plant manufacturer / supplier in China, offering 300tpd Wet Processing Cement Product Machine, Wet Process Cement Rotary Kiln for Calcined Dolomite in Cement Industry, Complete Cement Plant for 1000 Ton Per Day and so onChina 300tpd Wet Processing Cement Product The cement industry is the building block of the nation's construction industry Few construction projects can take place without utilizing cement somewhere in the design Annual cement industry shipments are currently estimated at $75 billion for 2012; up from $66 billion in 2011Cement Industry Overview

KHD provides semiwet process training to LH Volsk
The SIMULEX model for semiwet process was developed specifically for the Volsk project to simulate the plant production conditions realistically Besides providing the entire model for LafargeHolcim, the model will also be used for future training and service for other semiwet cement Portland cement for finishing brick buildings in wet climates; Mortars for masonry construction of harbor works, etc, in contact with seawater; Development of strong concretes; A cement is a substance used for construction, where mixed with fine aggregate produces mortar for masonry, or with sand and gravel, produces concretePrimary Process Control Improvements for Cement The cement milling process demands a major share of the total energy consumption of cement production This key performance indicator not only depends on the production rate and the specific fineness, but also on clinker quality and process efficiencyDevelopment of a linear statistical model for the

A MicroEconometric Model of Capital Utilization and
by adding water (the wet process) or without adding water (the dry process) The newer dry process preheats the kilnfeed before it enters the kiln So there are effectively three processes of cement production: wet, dry and drywithpreheater The production process of a kiln is irreversible The kilnfeed enters the kiln at one end and as it This paper focuses on modelling and solving the ingredient ratio optimization problem in cement raw material blending process A general nonlinear timevarying (GNLTV) model is established for cement raw material blending process via considering chemical composition, feed flow fluctuation, and various craft and production constraints Different objective functions are presented to acquire Modeling and Optimization of Cement Raw Materials There is a large cement distribution facility (now apparently closed) in West Sacramento CA, that could be represented in either N scale or HO scale using the appropriate Walthers Medusa Cement Kit A pretty accurate model could be made in N scale using the HO kit It had an overhead pipe line to deliver product to barges on the Sacramento RiverThe Cement Industry Model Railroad Hobbyist
- Lpgo Of Jaypee Wanakbori Cement Grinding Unit
- Hammer Crusher Wet Ore
- gypsum powder production line lahore pakistan
- crusher machine toggle
- Latest aggregate jaw crusher in algeria
- Buy A Used Rock Crusher Plant
- sodium lauryl internet
- attrition scrubbers crusher
- tracked mobile screening plant
- sand aggregate production flow diagram
- struktur mesin crusher pupuk drawing
- Crushing Plant Electrical Diagram Pdf
- stone crushing in ethiopia
- bisnis mobile menghancurkan dijual
- hydraulic granite crushing egypt
- kaolin beneficiation plant for chemical process
- 2015 hot sale stone crusher for crushing
- medical uses of titanium
- Mobile Crusher 150 250
- Jaw crusher For al ash asje Rock Jaw crusher
- australia widely used flotation pper ore mineral dressing
- platinum crusher mines
- a processing machines in lagos nigeria
- grinder machine in india for home purpose
- mills manufacturers crusherseation
- stone crusher portable machine
- crusher iron ore processing
- crusher harga pdf brosur
- specifications for super grinding machine
- crusher blades for lead plants
-
Primary mobile crushing plant
Independent operating combined mobile crushing station
Mobile secondary crushing plant
Fine crushing and screening mobile station
Fine crushing & washing mobile station
Three combinations mobile crushing plant
Four combinations mobile crushing plant
-
HGT gyratory crusher
C6X series jaw crusher
JC series jaw crusher
Jaw crusher
HJ series jaw crusher
CI5X series impact crusher
Primary impact crusher
Secondary impact crusher
Impact crusher
HPT series hydraulic cone crusher
HST hydraulic cone crusher
CS cone crusher
VSI6S vertical shaft impact crusher
Deep rotor vsi crusher
B series vsi crusher
-
Vertical grinding mill
Ultra fine vertical grinding mill
MTW european grinding mill
MB5X158 pendulum suspension grinding mill
Trapezium mill
T130X super-fine grinding mill
Micro powder mill
European hammer mill
Raymond mill
Ball mill
-
GF series feeder
FH heavy vibrating feeder
TSW series vibrating feeder
Vibrating feeder
Vibrating screen
S5X vibrating screen
Belt conveyor
Wheel sand washing machine
Screw sand washing machine