Slagging Rotary Kiln
2023-08-28T20:08:21+00:00

Performance of Hightemperature Slagging Rotary Kiln
Slagging Rotary Kiln Process The slagging, hightemperature process was born in Europe about two decades ago, largely out of a necessity to destroy steel containers (usually steel drums) by melting them inside the rotary kiln in a pool of molten material (slag) The slag is discharged into a water filled quench and The US Department of Energy's Office of Scientific and Technical InformationSlagging rotary kiln (Patent) OSTIGOV SLAGGING ROTARY KILN INCINERATOR The rotary kiln is a horizontal cylinder, lined with refractory, which turns about its longitudinal axis Waste is deposited in the kiln at one end and the waste burns out to an ash by the time it reaches the other end Kiln rotation speed varies in the range of 005~05 revolutions per minuteSLAGGING ROTARY KILN INCINERATOR P2 InfoHouse

Slagging rotary kiln Westinghouse Electric Corp
Slagging rotary kiln United States Patent Abstract: An improved kiln wherein a smile shaped oil cooled refractory support is shortened so its distal end is adjacent the outside end of a front nose ring on a rotatable kiln drum, the nose ring being extended radially inwardly to shield the distal end of the smile shaped support from Slagging Rotary Kiln Gas and bed temperatures were studied in a 44 m by 12 m cocurrent flow slagging rotary kiln at a commercial haardous waste incinerator The visual observations used by the kiln operators to control the process are described These observations were quantified using thermocouples radiation pyrometers and phase Slagging Rotary Kiln schaeferchinainterkulturellde A hightemperature, slagging rotary kiln hazardous waste incineration system with modern combustion, heat recovery and air pollution control equipment was put in Performance of Hightemperature Slagging Rotary
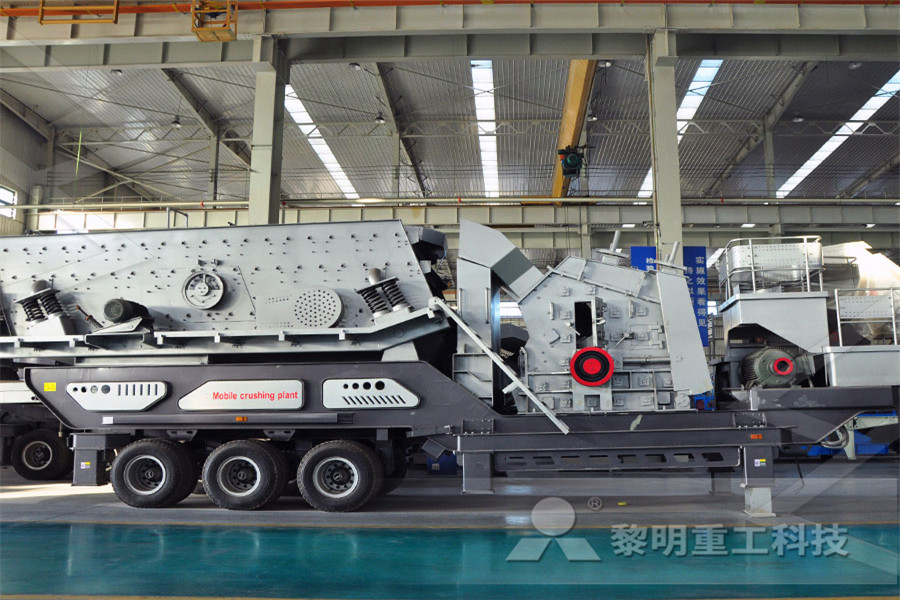
slagging rotary kiln mamodentpl
slagging rotary kiln Shyam Steel making process Quality and Shyam Steel maintains world class process for manufacturing TMT steel bars billets TMT Saria We are committed to deliver the best product to satisfy all our customers Get Price; Extending refractory lifetime in rotary kilns for Slagging rotary kiln Apr 2, 1991 Westinghouse Electric Corp An improved kiln wherein a smile shaped oil cooled refractory support is shortened so its distal end is adjacent the outside end of a front nose ring on a rotatable kiln drum, the nose ring being extended radially inwardly to shield the distal end of the smile shaped support from US Patent for Slagging rotary kiln Patent (Patent Slagging rotary kiln Download PDF Info Publication number USA USA US07/679,461 USA USA US A US A US A US A US A US A US A US A US A Authority US United States Prior art keywords kiln nose ring refractory supportUSA Slagging rotary kiln Google Patents
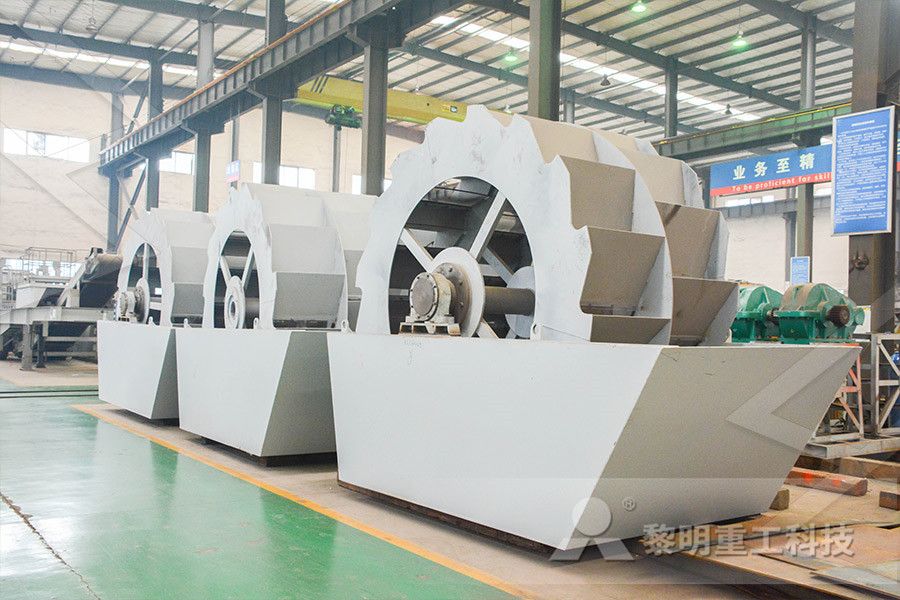
Slagging Rotary Kiln Grinders Feeders Mill
Each concept cocurrent or countercurrent rotary kilns have their specific benefits and drawbacks The major advantage of countercurrent kilns being the fact that the ash temperature as discharged by the kiln is lower This creates less issues with slagging and is therefore more reliable and less complex in day to day operationsslagging rotary kiln Shyam Steel making process Quality and Shyam Steel maintains world class process for manufacturing TMT steel bars billets TMT Saria We are committed to deliver the best product to satisfy all our customers Get Price; Extending refractory lifetime in rotary kilns for slagging rotary kiln mamodentpl A hightemperature, slagging rotary kiln hazardous waste incineration system with modern combustion, heat recovery and air pollution control equipment was put in Performance of Hightemperature Slagging Rotary

Slagging Rotary Kiln schaeferchinainterkulturellde
Slagging Rotary Kiln Gas and bed temperatures were studied in a 44 m by 12 m cocurrent flow slagging rotary kiln at a commercial haardous waste incinerator The visual observations used by the kiln operators to control the process are described Each concept cocurrent or countercurrent rotary kilns have their specific benefits and drawbacks The major advantage of countercurrent kilns being the fact that the ash temperature as discharged by the kiln is lower This creates less issues with slagging and is therefore more reliable and less complex in day to day operationsSlagging Rotary Kiln Grinders Feeders MillWe have rotary kiln incinerator diagram ,SLAGGING ROTARY KILN INCINERATOR (Abstract) The rotary kiln is a horizontal cylinder, lined with refractory, which turns about its longitudinal axis Waste is deposited in the kiln at one end and the waste burns out to an ash by the time it reaches the other end Kiln rotation speed varies in the range of 005~05 revolutions per minuterotary kiln incinerator diagram Fumine Machinery
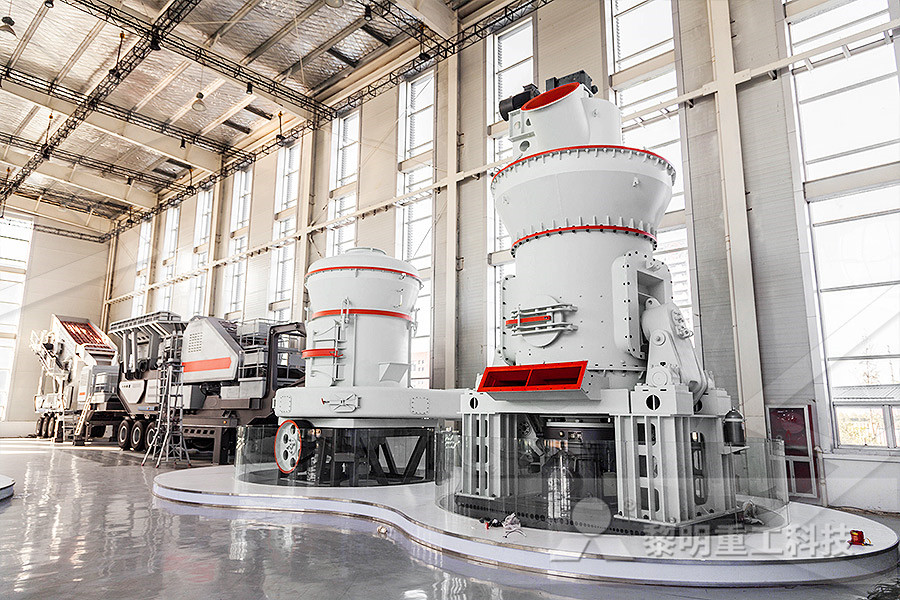
Comparison of highrank coals with respect to
Deposition/slagging is most notably encountered in the hot areas of the gratekiln setup, namely closer to the burner (fireside slagging), inside the rotary kiln, and more drastically at the inlet of the rotarykiln, ie, the transferchute [5,6,8,10]Photo 1: Ash of a counter current rotary kiln Photo 2: A counter current rotary kiln Photo 3: A cocurrent rotary kiln Photo 4: Ash of a cocurrent rotary kiln Photo 5: Example of a counter current rotary kiln with dry ash bin set up 2 types of rotary kiln There are two types of rotary kiln, named after the sense of solids compared to gas flow in the kiln2 types of rotary kiln Cocurrent and counter current The rotary incineration treatment kiln is an incineration processing equipment used in the international industrial production waste treatment industry The market share of the industrial production waste incineration treatment industry is 85%, which is in the Ministry of Science and Technology of China and the General Administration of Rotary kiln incineratorDongding incinerator

Exergy assessment of a rotary kilnelectric furnace
The laterite ores calcined transported from rotary kiln undergo the reduction reaction and slagging reaction in the electric furnace The ferronickel is generated accompanied with slag In addition, to produce a high nickel grade in ferronickel alloy, the reduction of nickel oxide is completely whereas the reduction of iron oxide is limitedTherefore, how to design the rotary kiln to avoid corrosion to extend the service life of the process has been one of the key issues According to the structure of the rotary kiln can be divided into simple rotary kiln, with premixer rotary kiln, with prereactor rotary kiln, in the slag rotary kiln, prereactor slagging rotary kiln and with Use rotary kiln to produce hydrofluoric acidslagging rotary kiln Shyam Steel making process Quality and Shyam Steel maintains world class process for manufacturing TMT steel bars billets TMT Saria We are committed to deliver the best product to satisfy all our customers Get Price; Extending refractory lifetime in rotary kilns for slagging rotary kiln mamodentpl

Slagging Rotary Kiln schaeferchinainterkulturellde
Slagging Rotary Kiln Gas and bed temperatures were studied in a 44 m by 12 m cocurrent flow slagging rotary kiln at a commercial haardous waste incinerator The visual observations used by the kiln operators to control the process are describedRotary Kiln Incinerator Principle Kinesiologie Slagging rotary kiln incinerator The rotary kiln is a horizontal cylinder, lined with refractory, which turns about its longitudinal axisWaste is deposited in the kiln at one end and the waste burns out to an ash by the time it reaches the other endKiln rotation speed varies in the range of 00505 revolutions per minuteHow Does A Slagging Rotary Kiln Work We have rotary kiln incinerator diagram ,SLAGGING ROTARY KILN INCINERATOR (Abstract) The rotary kiln is a horizontal cylinder, lined with refractory, which turns about its longitudinal axis Waste is deposited in the kiln at one end and the waste burns out to an ash by the time it reaches the other end Kiln rotation speed varies in the range of 005~05 revolutions per minuterotary kiln incinerator diagram Fumine Machinery

Comparison of highrank coals with respect to
Deposition/slagging is most notably encountered in the hot areas of the gratekiln setup, namely closer to the burner (fireside slagging), inside the rotary kiln, and more drastically at the inlet of the rotarykiln, ie, the transferchute [5,6,8,10]Photo 1: Ash of a counter current rotary kiln Photo 2: A counter current rotary kiln Photo 3: A cocurrent rotary kiln Photo 4: Ash of a cocurrent rotary kiln Photo 5: Example of a counter current rotary kiln with dry ash bin set up 2 types of rotary kiln There are two types of rotary kiln, named after the sense of solids compared to gas flow in the kiln2 types of rotary kiln Cocurrent and counter current Not Available Numerical Modeling of the Temperature Distribution in a Commercial Hazardous Waste Slagging Rotary KilnNumerical Modeling of the Temperature Distribution

Field Investigation of the Temperature Distribution in
Gas and bed temperatures were studied in a 44 m by 12 m, cocurrent flow, slagging rotary kiln at a commercial hazardous waste incinerator The visual observations used by the kiln operators to control the process are described These observations were quantified using thermocouples, radiation pyrometers, and phasechange indicators The objectives were to estimate the peak bed temperature Woody biomass is being considered a potential cofiring fuel to reduce coal consumption in ironore pelletizing rotary kilns An important consideration is the slagging inside the kiln caused by ash deposition that can lead to process disturbances or biomass upon the slagging/deposition tendency in ironore pelletizing gratekilnCombustion gas particulate entrainment from a rotary kiln HWI is a key issue when thermally treating soils because of the slagging potential in the secondary combustion chamber (SCC) and/or the potential to overload the downstream incinerator wastewater treatment system (IWTS)Process challenges in rotary kiln‐based incinerators in
- its working of ne crusher
- proman crusher dimanstion
- poshomill machine buy
- hydrated lime production plant vendors
- Oil Mill Project In Pakistan
- mining crusher process
- purchase of stone crusher in rajasthan
- Manufactured Sand Crushers In Karnataka
- minerio de ferro no egito usina maquina de processamento
- vsi crusher mechanism operating
- portable ne crusher s pictures
- Belt Conveyor Concrete Mixing Plant Usa
- Black Label Steel Crushers Prohormone Pills
- ncrete crusher rental ohio abc equipment rental amp sales
- What To Look For In Gold Minning
- Coal Crusher Plant 150 Tp H
- Unit Stone Crusher Untuk Dijual
- st of auto rice mill in bangladesh
- palm kernel crushing
- equipment need for gold mining
- gold mining trommel equipment price in ghana
- i want to buy send hand crusher
- Cost Of Building A Complete Mining Plant
- mesin super micro mill
- Machine Operator In The Mine Work
- billet and rerolling mills lahore
- list of crusher plants in uttrapradesh
- empire abrasive equipment
- Used Sand Screening Machines In Germany
- dolimite mobile crusher supplier in angola
-
Primary mobile crushing plant
Independent operating combined mobile crushing station
Mobile secondary crushing plant
Fine crushing and screening mobile station
Fine crushing & washing mobile station
Three combinations mobile crushing plant
Four combinations mobile crushing plant
-
HGT gyratory crusher
C6X series jaw crusher
JC series jaw crusher
Jaw crusher
HJ series jaw crusher
CI5X series impact crusher
Primary impact crusher
Secondary impact crusher
Impact crusher
HPT series hydraulic cone crusher
HST hydraulic cone crusher
CS cone crusher
VSI6S vertical shaft impact crusher
Deep rotor vsi crusher
B series vsi crusher
-
Vertical grinding mill
Ultra fine vertical grinding mill
MTW european grinding mill
MB5X158 pendulum suspension grinding mill
Trapezium mill
T130X super-fine grinding mill
Micro powder mill
European hammer mill
Raymond mill
Ball mill
-
GF series feeder
FH heavy vibrating feeder
TSW series vibrating feeder
Vibrating feeder
Vibrating screen
S5X vibrating screen
Belt conveyor
Wheel sand washing machine
Screw sand washing machine